石化机械:自主研发锻造油气领域“国之重器”
更新时间:2024-08-01 05:33:58
作者: 传动机械设备铸件
能源产业的发展离不开石油装备制造产业的突破,而要真正的完成能源产业的健康发展、维护国家能源安全,掌握装备制造产业的核心技术必不可少。
作为中国石化下属唯一油气装备研发、制造与专业方面技术服务中心,中石化石油机械股份有限公司(简称:石化机械)是我国“石油系”主要的设备制造商之一,始终以打造“国之重器”、服务能源发展为使命,深度融入中国石化“一基两翼三新”产业格局,扛稳保障国家能源安全使命责任。本版详细的介绍石化机械重点产品的研发及应用成果,敬请关注。
时隔6年,2022年,我国原油产量重回2亿吨“里程碑”,同时,天然气储量、产量也实现较大幅度增长。能取得这样亮眼的成绩,得益于勘探开发技术的不断的提高,也离不开油气装备制造企业的锐意创新与大力支撑。
作为中国石化唯一油气装备研发、制造与专业方面技术服务中心,石化机械从始至终坚持面向油气勘探开发痛点、现场作业难点、提速提效堵点,不断推进自主技术创新,持续推动中国石化石油工程产品产业化建设,牵头打造油气装备产业化基地。
“2022年,我们自主研制的连续满载全电动压裂成套装备、油气装备集中控制管理系统、储气库压缩机、金刚石钻头等6次亮相央视荧屏。”该公司CEO王峻乔说。如今,石化机械数字化转型措施结出累累硕果,关键装备工具一揽子解决方案及一大批技术先进、高效可靠的国产油气装备工具,正为我国深地、页岩油气、深水油气勘探开发提供有力支撑。
相比页岩气,页岩油开发是一场新的革命——压裂施工进一步由“井工厂”模式向大平台水平井工厂化拉链式压裂转变,开发难度更大、对装备要求更高,需要出示更大液量和压力。
“压裂可使地层产生裂缝,对改善油气井井底流动条件、油层动用状况起到及其重要的作用,能有效增加油气产量。水平井钻井技术与水力压裂技术的结合,可从根本上解决页岩油气致密性强、渗透率低、流通性差的问题,实现在更大的三维立体空间开采致密油气。”王峻乔介绍,随着页岩油勘探开发在我国陆上、海上取得突破,大功率压裂机组的发展也迎来了新的机遇和挑战。
赶超国外先进的技术,开发具有自主知识产权的大型压裂装备,是几代油气装备人的使命与担当。早在“十二五”时期,石化机械就牵头实施国家科技重大专项“3000型成套压裂装备研制及应用示范工程”,取得的“超高压大功率油气压裂机组研制及集群化应用”成果荣获国家科学技术进步二等奖,首创的3000型车载压裂装备在涪陵国家级页岩气示范区建设中大展身手,并推出了页岩气开发关键装备及工具一体化解决方案。
然而,传统柴驱压裂装备噪声大、作业成本高、污染物排放多,怎么样才可以做到“这里的黎明静悄悄”?着眼深层页岩气绿色低碳开发,石化机械牵头承担了国家“十三五”科技重大专项“深层页岩气开发关键装备及工具研制”任务,相继推出油电混合、超大功率全电动、连续满载全电动压裂成套装备,使压裂效率提高1倍以上、综合成本下降30%。不仅应用技术入选国家绿色技术推广目录、央企科学技术创新成果推荐目录,而且该装备分别亮相国家“十三五”科学技术创新成就展、庆祝改革开放40周年大型展览,被永久收藏于国家博物馆。
如今,以压裂泵、混砂装置、高压管汇、控制管理系统等为核心,石化机械建成国际领先水平的成套压裂装备技术体系,超大功率连续满载全电动压裂成套装备成为页岩油大平台工厂化施工、连续满载作业的最优选择,已顺利完成江苏油田花2侧HF井、国家级页岩油示范区樊页1试验井组压裂施工,创下多项优异指标,为页岩油开发规模化应用立下了汗马功劳。
2022年12月28日,中国石化部署的风险探井元深1井顺利完成钻井深度8866米,到达目前四川盆地埋深最深的油气层。一年之内,“深地工程”接连获得突破,这其中就有油气装备的功劳。
近年来,深层、超深层油气资源已变成全球和我国油气发现的主阵地。要揽“瓷器活儿”,得有“金刚钻”。看似不起眼的钻头,实则是油气装备领域的“小巨人”。面对油气藏超深、高温、高压工况,石化机械针对性开发出长寿命、耐高温钻头钻具和7000米自动化钻机、9000米超静定钻机、自动化连续油管作业装备、2500型固井车等关键核心产品,为深地油气勘探开发提供了有力的装备支撑。
深部钻探,钻头钻具是影响工期和成本的关键。聚焦砂砾岩、火山岩等难钻地层的提速难题,石化机械开发了混合钻头、异形齿钻头、孕镶钻头、双心钻头等,稳定性和工况适应性明显提升。特别是“龙系列”混合钻头,对定向井和硬地层、夹层、砾石层等具有广泛适用性,已成为钻井提速利器,累计完成超7000趟次钻井作业。第二代“龙”系列混合钻头提速效果、适应能力逐步提升,机械钻速平均提高25%以上、进尺平均提高50%以上、常规使用的寿命延长75%以上,其中直径444.5毫米混合钻头轴承寿命更是达到200小时以上。
同时,该公司开发的等壁厚螺杆可为钻头提供破岩扭矩,大范围的应用于水平井、定向井、超深井钻井作业,在大扭矩、耐油基、耐高温、高转速、长寿命、可靠性方面均实现了突破;旋转导向螺杆融入低速大扭矩马达、超高硬度橡胶、高承载传动系统、高强韧性金属材料等技术,进一步满足了长水平段—复杂井眼轨迹钻井、螺杆钻具匹配旋转导向系统的提速需求。
随着大数据、云计算等信息技术在石业应用,智能钻机已成大势所趋。石化机械紧跟行业发展的新趋势,积极开展“超深井安全高效钻井关键装备研制与应用”项目攻关,首创超静定结构弹弓式底座,创下了国内钻机底座13.7米高度纪录;研制的9000米钻机应用了高净空高稳定底座、轻量化井架及集成控制管理系统技术,可适应各类工况作业,解决了超深层油气井高压防喷器组安装和钻机高承载稳定性难题;开展的“7000米自动化钻机联合研制及应用示范”项目攻克了钻柱自动排放运动机理、钻柱自动识别与定位等关键核心技术,开发出“推扶式”钻柱自动排放系统、管柱自动处理、自动化工具集成控制、钻机快速移运装置等关键技术和装备,让“以机代人”不再是梦。
“下一步,我们要继续完善智能钻井闭环链,推进钻井领域全面自动化,逐步提升钻井效率、降低作业强度和危险系数。”王峻乔说。
压缩机种类非常之多,是天然气增压开采、气举排液、集中处理输送、注气加气和各利用领域都要用到的关键设备。
依托数十年的压缩机制造优势,石化机械建成了压缩机国产化制造基地,以市场需求为导向,强化自主技术创新,联合国内外优势技术资源,开展压缩机控制、仿真分析等研究,攻关压缩机关键制造技术,不断拓展RDS压缩机系列。特别是近年来,页岩气增压压缩机、高压大功率储气库压缩机、二氧化碳压缩机、高含硫天然气压缩机、海洋大功率往复式压缩机、氢气压缩机等特色装备应运而生,大幅度提高了压缩机自主化率并明显降低成本,广泛应用于国内油气田开发。
在普光气田,面对高含硫压缩机对抗腐蚀性、密封性、安全性的高要求,石化机械从结构设计、耐腐材料、焊接工艺、整机试验等维度入手,突破关键核心技术难题,在国内率先掌握适用于含硫化氢17.5%天然气环境下运行的压缩机研发与制造技术,打破国外垄断。2022年4月,该公司推出的国内首台高含硫天然气压缩机组,在普光气田P101站完成工业化试验,为酸性气田开发、稳产增产提供了装备支撑。
利用二氧化碳驱油,可开发低渗透油藏储量,实现温室气体减排和资源化利用,而把二氧化碳注入油层的关键装备就是压缩机。针对运行过程中二氧化碳含量变化范围广、压力大的特点,石化机械攻关研制具有抗酸性并适用于超临界状态的高端压缩机组,解决了机组转速范围调节、反向角变化、载荷比分布、二氧化碳腐蚀等问题,满足了二氧化碳回注需求,并成功应用于我国首个百万吨级CCUS(碳捕集、利用与封存)项目——齐鲁石化-胜利油田CCUS项目。
在北京冬奥会开幕式上,中国石化的氢点燃了主火炬,人们的目光再一次聚焦氢能。在发展氢能产业方面,油气公司具有独特的先天优势。面向氢能利用,石化机械依托天然气压缩机、自动化控制等装备技术积累,开展氢能装备行动,全力打造氢能关键装备的研发、制造和服务基地,重点布局加氢、制氢装备市场。该公司自主研制加氢站压缩机、注氢机等关键设备,集成制造的45兆帕加氢站成套装备已在中国石化武汉群力综合能源站开始注氢调试,即将开展加氢服务;90兆帕氢气压缩机、35兆帕加氢机、顺序控制盘、站控系统等产品完成试制,氢能装备制造基地一期工程建设完成,将建成国内首条氢能压缩机全工况测试线,模拟实际工况下测试产品性能,保障出厂产品安全可靠。
未来,石化机械将坚定走“核心技术+关键制造+专业服务”的发展路径,深入实施“培育单项冠军,推进两个转型,打造百亿企业”战略,持续建设技术先导型企业,扛稳保障国家能源安全使命责任。
石化机械持续提升服务用户能力和企业可持续发展能力,培育形成钻完井工具一体化服务、设备租赁、设备健康管理、装备改造运维、泵送与增压等特色服务,在促进工程“四提”“五化”、提高上游装备本质安全水平等方面发挥了重要作用,也得到了更多用户的认可与好评。
■相较于国内同类产品高冲次大功率(178冲/分)、最高压力120兆帕的设计,相同功率下,石化机械连续满载全电动压裂成套装备低冲次大功率(87冲/分)、最高压力140兆帕,产品冲次下降了51%,泵头寿命在1000~1500小时,高压管汇安全系数提升了11%~13%,装备运行综合成本下降24%,压裂泵作业功率提升16%,检泵周期延长100%,由10段提高至20段;配备自动检泵工具,检泵维护时间缩短40%。配套“压裂井场全流程自动化控制系统”,可实现液罐液位远程监控和倒换流程远程控制。
胜利石油工程:石化机械制造的超大功率连续满载全电动压裂成套装备,解决了连续满载长寿命压裂泵、小体积交流变频、超高压大通径管汇、电动直驱混排、一键式全流程控制等技术难题,实现了电驱压裂、电动配液、电动输砂等全流程24小时连续作业,具备单泵排量大、施工效率高、故障率低、满足连续施工需要等优势,有效满足了樊页1试验井组页岩油开发施工需要。
■卫11储气库压缩机是石化机械自主研发、“全自主化”制造的高端压缩机,形成高压动密封、大交变应力汽缸结构设计、多机联运振动控制、精准注油系统集成、高功率能耗优化等特色技术,具有压力高、排量大、适用范围广、安全可靠、振动小、噪声低、能效高、智能运维和服务响应快等特点。
:卫11储气库建设时间紧、任务重、责任大,石化机械全力推动压缩机设计、生产、安装提速,全面优化工艺流程,为项目顺利完工提供了强有力的设备支撑。从卫11储气库到胜利油田永21储气库,石化机械积极响应中原储气库群建设需求,制造的23台大型压缩机组在9个气田成功应用,并精心提供运维服务,现场开展故障诊断修复工作,全面保障了储气库压缩机运行、维护和配件供应,为压缩机组“安稳长满优”运行提供了有力保障。
■石化机械大力探索推行以全井和井段承包等为核心内容的钻头钻具一体化服务,面向深井、超深井和页岩油气勘探开发等特殊井与复杂地层有关需求,针对性开发钻头钻具,主动向钻井客户提供一揽子产品和服务,有效助力油气勘探开发超深井提速提效,受到钻井用户广泛认可与好评。
中国石油川庆钻探工程公司:塔里木富源3-H3井应用石化机械“尖峰”“先锋”金刚石钻头、硬地层混合钻头,匹配大扭矩螺杆钻具,实现一体化提速,完成8136米进尺任务,机械钻速9.4米/小时,全井周期113.67天,较设计周期节约68.33天,刷新同区块同类型单井最短周期施工纪录。
问:目前,我国油气装备制造业发展情况如何?在支撑油气勘探开发方面,还存在哪些困难和不足?
答:经过数十年创新发展,我国油气装备制造已取得了长足进步,整体设计、制造水平位于世界前列。钻井装备形成了以深地钻机、自动化钻机和高效钻头钻具等为代表的系列化新产品;全电动压裂、无水压裂装备日益成熟;修井装备电动化、自动化成效明显,最大作业深度已经突破9000米;连续管作业装备基本满足国内油气田生产需求;测录定工具仪器全面实现自有化;高压注气压缩机、高含硫压缩机等不断挑战开发条件极限;钛合金油套管、铝合金钻杆等特殊管的应用规模持续扩大;形成第三代大输量天然气管道工程、高钢级管道完整性等关键装备技术。
目前,我国油气装备能够满足油气田生产需求,但大功率发动机、传动箱等部件仍依赖进口,自动化、智能化、信息化程度也有待提高。在自动化钻井装备、深海油气开发技术装备、超高温井下工具等高端装备方面,还存在“卡脖子”技术瓶颈,影响我国油气高效勘探和效益开发。
问:中国石化的油气装备研发制造能力在行业内处于什么水平?下一步将如何发展?
答:作为中国石化下属唯一油气装备研发、制造与专业技术服务中心,石化机械多年来坚决扛稳扛牢打造大国重器、支撑油气发展的责任担当,坚持创新引领,持续推动我国油气装备走出一条高水平科技自立自强之路。以国家“十二五”“十三五”科技重大专项为依托,我们立足钻井工程、井下作业、油气集输三大工程领域,围绕非常规油气、超深层油气开发,形成了关键装备工具一揽子解决方案,研制出全电动压裂装备、大功率自动化固井装备、自动化钻修井机、系列高效钻完井工具、多种介质增压压缩机等领先产品,助力更高水平的涪陵页岩气田商业化建设和更高质量的塔里木深地油气工程勘探开发。
面向未来,我们将聚焦非常规油气、深地、深海、CCUS等领域勘探开发需求,致力于油气装备自动化、智能化迭代升级,攻关打造智慧固井压裂装备、智能化钻机、超深超高温超高压钻井工具仪器、二氧化碳压缩机等高端产品,搭建油气装备智能物联平台,实现装备全生命周期健康管理。聚焦“双碳”目标,瞄准氢能装备领域,推动制氢装备、氢气压缩机等研发。
装备制造业属于典型的离散制造业,由于产品结构复杂、研制周期长、物料品种规格多,管理难度较大。
产品的生命周期进一步缩短,促使企业不断加快新产品开发与新技术应用,确保新产品能在最短时间上市。
我国已成为制造业大国,装备制造业既迎来发展机遇,又面临国内外强大的竞争压力。如何在技术、成本、质量、服务等方面增强竞争力,是装备制造企业亟待解决的问题。
原材料价格不断上涨、生产费用增加,导致装备制造业的盈利能力较弱,企业必须想方设法有效减少相关成本。
对客户需求响应的要求变得越来越高,需要企业缩短产品研发周期、采购提前期和制造期,提高柔性制造水平,这些都导致研制能力成本增加,也对劳动力提出了更高要求。
- 电话:15028752820
- 邮箱:info@zhugang.com
- 地址:河北省泊头市千里屯工业区199号
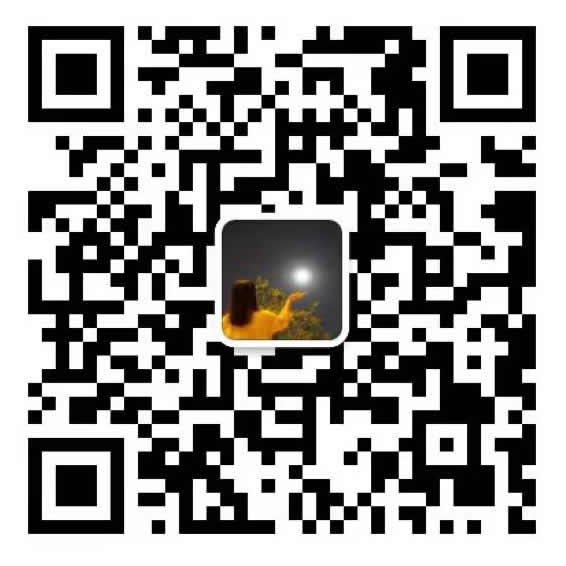
冀公网安备 冀ICP备17001371号-5
Copyright © 2002-2020 bob官方平台app_bob线上官网 版权所有 XML地图