谈铸钢熔炼方面的几个问题
更新时间:2025-04-28 12:22:22
作者: 传动机械设备铸件
近10年来,我们国家的国民经济发展很快,铸钢件产量随之大幅度增长。1998年,各类铸钢件产量为130.4万t,2008年飙升至460万t,多于俄、美、印、巴西、日、德、韩、法、意、英等10国铸钢件产量的总和。在产品品种和质量方面,也取得了很多可喜成果。在大型铸钢件方面,我们制成了水电站用超大型不锈钢铸件、大型超超临界汽轮机用铸钢件。2008年,中信重工机械公司制造了当今世界上最大的铸钢件,重520t的大型液压机横梁。小型铸钢件方面,在航空用燃气轮机单晶叶片方面也有了重要进展。但总体而言,铸件质量档次不高仍是我国铸造行业的“软肋”,特别是在铸件内在质量方面,与其他工业国家相比,仍有很大差距。在国际市场的竞争主要靠低价格(铸件价格,大体上是其他工业国家同种类型的产品价格的一半),故此,我国铸造企业的利润很小。大多数企业在研究开发、技术改造、改善劳动条件和环境治理等方面心有余而力不足,我国铸造行业一时难于摆脱落后局面。在以世界上前所未有速度发展的过程中,失之粗放在所难免,不过我认为,现在已经到了“从量到质、由表及里”的阶段了。决不能盲目满足于表面业绩,沾沾自喜于量的增长。“苦练内功、提高铸件质量”,才是我们提升产品竞争能力的根本所在。也是我国从‘铸造大国’走向‘铸造强国’的必由之路。基于如此认识,拟就铸钢熔炼方面的三个问题,提出些粗浅看法,盼与铸钢业界同仁探讨之。
生产“清洁钢”一直是各国铸钢业界广泛关注的问题。为进行这方面的研究,已花费了可观的时间、金钱和人力。对铸钢业界,生产“清洁钢”的含义是:加强脱氧和防止出钢和浇注过程中的二次氧化,从而避免铸钢件的气孔缺陷,减少钢中非金属夹杂和铸件表面的氧化夹杂。说起来,这是个老问题,从事铸钢的人都知道,但实际上很多人对此并无切实的认识。
谈及的只是最初步、最基本的内容。在钢液精炼方面,无论是化学成分,钢中的非金属夹杂物含量、形态和分布状况,气体含量等,都必须与铸件的质量发展要求相适应。工业生产里,要讲究“价值工程”。对于铸钢件的冶金质量,既不能得过且过,也不能离开产品的规格要求盲目攀高。目前,我国铸钢业界已有不少企业装备有炉外精炼设施,可生产高端产品,这方面的冶金质量发展要求,大都较特殊,无普遍意义,故不在此讨论。本文中所谈的“清洁钢”,仅指“充分脱氧”,这是生产各种、各类铸钢件时都必须做到的。近20年来,
充分脱氧的重要性炼钢过程中,钢液氧化不可避免。一般说来,氧化是炼钢过程中必不可少的精炼手段,脱氢、脱氮、清除非金属夹杂物,都必须借助于氧化脱碳。但氧化毕竟只是炼钢手段,钢炼好后,就必须将氧完全脱除,否则就会严重损害钢的质量。就像医生用精良的手术刀完成手术后不可将手术刀留在患者体内一样。采用不氧化法炼钢时,虽然并不故意向钢中加氧,但在熔炼过程中钢不可避免地会被大气中的氧所氧化,所用的各种原、辅材料也会给钢液中带进氧,脱氧仍然是炼钢作业中的关键。充分脱氧当然还包括认真防止二次氧化,使进入铸型的钢液脱氧充分。1.2脱氧不充分会导致铸件中产生气孔若熔炼终了时钢液脱氧不充分,再加以出钢、浇注过程中液流的二次氧化,钢液进入铸型后,金属/铸型界面处钢液中的FeO含量较高,随凝固进行和钢液温度下降,钢中所含FeO就会与碳反应,产生CO,在铸件中形成皮下气孔。正常的情况下,碳氧反应是铸件产生气孔的根本原因。钢中FeO与碳的反应是吸热反应,为什么在温度下降、铸件已开始凝固时,能发生反应、造成气孔呢,早年,该问题曾被视为冶金学之谜。现在,从扩散传质、偏析和表面现象来分析,可有较清楚的认识。在均匀的液相中产生气泡是十分艰难的,需要给予能量使系统自由能增加。钢是以“硬皮形成”方式逐层凝固的合金,钢液浇注到铸型中后,钢液/铸型的界面上很快就形成一层硬皮,这层硬皮是由很多垂直于界面、尖端向内的细小柱状晶构成的。柱状晶的端部很尖,具备极高的表面能,而且附近又有因体积收缩而造成的微小孔隙,这两点都为CO气泡的生核、长大准备了外部条件。随着初生晶体的析出,晶粒表面附近钢液中的碳含量增高,形成富碳层,同时,因温度下降和初生晶粒析出,1.1
富碳钢液中FeO含量也提高。这就是反应能够发生的内因。CO气泡形成后,对氢和氮而言,气泡是真空,本来可固溶于钢中的氢和氮也会向其中扩散,使气泡体积扩大,造成皮下气孔。
炉渣中FeO量保持在0.5%以下。无论用电弧炉或感应电炉炼钢,都有此要求。几年前,我们曾在铸钢专业会议上提出这一问题,有的企业很重视,认真做到了,并取得了很好效果。但大多数企业对此仍缺乏正确认识,不少铸钢厂出钢前炉渣中FeO量都在1%以上,甚至有高达2%的,能达到0.8%的为数不多。而且,大多数铸钢厂从来就不检测炉渣中FeO量,这样的一种情况的确应尽快改变。一般地,终脱氧都是出钢时在钢包内进行。广泛采用的终脱氧剂是铝。用铝进行终脱氧时,铝的加入量应严控在0.08%到1.2%之间,加入法也要严格一致。目前,很多铸钢厂终脱氧用的铝都不称量,由操作人员凭经验取用,加入法也很随意,这是极不正常的做法,可不少企业却习以为常。()只用硅、锰脱氧1如果只用硅、锰脱氧,不用铝进行终脱氧,或加铝量很少,钢中含有大量SiO2和MnO,二者又能结合成硅酸盐,这类非金属夹杂物以球状析出,零乱分布。此外,锰也与硫反应生成MnS。MnS在钢中的溶解度与钢中的氧含量有关,氧含量高,则MnS的溶解度下降。在钢液脱氧不充分时,硫化物夹杂于凝固初期形成,呈球状或不规则的粒状。这类非金属夹杂-型夹杂物,见图1。(包括硅酸盐和硫化物通常称为Ⅰ)这类夹杂物对钢的力学性能影响不大,但在此种冶金条件下,钢液脱氧不充分,铸件不可避免地会产生气孔。因而,对于生产铸钢件,是一定不可以采用这种脱氧方式的。
脱氧不充分会使铸钢力学性能恶化若钢液脱氧不充分,其中的FeO量较高,虽不至于形成气孔,但由于FeO在钢液中溶解度高,在固态钢中溶解度低,钢结晶过程中析出的FeO会偏析于晶粒边界,使钢的韧性和塑性降低,力学性能恶化。钢液中氧含量高,也会影响钢中氧化物、硫化物夹杂数量和分布状况,进而影响钢的力学性能。1.4脱氧不充分会使铸件的表面缺陷增多铸钢件表面缺陷(如粘砂、结疤、夹渣、皱皮、沟槽等十分常见,清除缺陷和焊修是必不可少的工)序。根据国外的统计分析,铸钢件直接生产所带来的成本中,清理铸件表面缺陷的费用约占20%,其中,大部分被用于清除氧化夹杂物缺陷和焊修。一般铸造厂,往往 把这类缺陷的产生归咎于浇注和造型。粗看起来,似 无可非议,深究起来,并非如此。 为弄清铸钢件表面缺陷多的原因,美国铸钢研究学 会曾组织一些铸钢企业和高等学校人员进行大量研究, 从各类铸钢件 ( 包括碳钢铸件、低合金钢铸件和中、高 合金钢铸件 中取样500件以上,做多元化的分析研究,结果 ) 表明,铸件表面宏观夹杂的来源如下:因钢液脱氧不充 分和二次氧化造成的占83%;来自造型材料的占14%; 来自炉渣的占2%;来自耐火材料的只占1%。 钢液/炉渣界面处的FeO与硅砂作用,可形成熔点 为1 250 ℃左右的硅酸盐,甚至熔点更低的共晶体,从 而在铸钢件表面上形成宏观氧化物。因此,铸钢件的 清洁度,可用每吨铸件表面需清除的宏观夹杂体积来 衡量,也可用每吨铸件修补所用的焊条量来衡量。当 然,钢中微观夹杂的数量,形态及分布状况也与其清 洁度相关,但对一般铸钢件而言,这种影响可不计较。 美国铸钢研究学会在许多铸钢厂现场进行的调查 表明,不同炉次间的铸件,每吨铸件修补所需焊条量 差别很大;同一炉次浇注的铸件,从最先浇注的到最 后浇注的,每吨铸件焊条用量差别不大。而且,铸件 宏观夹杂多的炉次约占20%~25%。这说明,熔炼方面 容易失控的变数较多,而浇注过程中的变数较少。因 此,加强脱氧和防止二次氧化是当前铸钢业应予以特 别关注的问题。 1.5 钢液的脱氧要求 目前,对铸钢件浇注过程中的二次氧化尚缺乏有 效的防止方法,尤其应使钢液在炉内脱氧良好。日本 铸钢业界人士的说法是,熔炼过程应使钢液具有充分 的脱氧余力。国外铸钢业界一般都在严控还原作 业的基础上,要求出钢前,也就是加铝进行终脱氧前, 1.3
() 终脱氧加铝量不足 2 用硅、锰脱氧后,用铝进行终脱氧,铝加入量在 0.025%~0.05%之间时,钢中残留铝量约为0.01%~0.03%。 这种情况下,钢中FeO量较低,MnS ( 其中有少量FeS 与之形成复合化合物 在钢中溶解度增高,因而不在 ) 钢凝固初期析出,浓集于液相中,最后,以网膜状析 出于晶粒边界。这种分布状况的夹杂物称之为Ⅱ -型夹 杂物,如图2所示。钢中有这种夹杂时,其韧性、塑性 都很低。因此,这种终脱氧方式也不允许。 () 应严控终脱氧加铝量 3 如用硅、锰脱氧后,再加入较多铝 (0.1%左右 ) 进 行 终 脱 氧 ,钢 中 残 留 铝 量 超 过 0.04% , 就 可 形 成 Al2S3。Al2S3也可与MnS、FeS形成复合硫化物。这种复
中,以小块铝逐个投入液流,或将铝块固定在钢棒上 插入钢液,都是可行的做法。国外有的铸钢厂不直接 用铝,而将铝预制成含铝35%左右的铝铁合金,密度 约为6.15 g/cm3,高于炉渣,与钢液相近。虽然成本略 高,但脱氧效果较好且稳定。
合硫化物在钢液中溶解度很低,析出于钢液凝固早期, 颗粒尺寸较大,形状也不圆整,但主要分布在晶粒内 部,很少在晶界析出,对钢的力学性能影响较小。这 种夹杂物称之为Ⅲ-型夹杂物,如图3所示。
钢液终脱氧所用加铝量,当然要考虑脱氧效果及 其对夹杂物形态和分布状况的影响。不加铝,则既不 能使钢充分脱氧,又不能细化晶粒;用铝作终脱氧剂, 但加入量不足以使钢中的残留铝量超过0.04%,钢中就 也许会出现有害的Ⅱ -型夹杂物。因此,用铝作终脱氧剂 时,其加入量的下限为0.08%不难理解。 既然铝是强脱氧剂,且加入量少了不行,多加岂 不更好,为何还规定上限?铸钢件发生一种特殊脆断 的情况时有所闻。厚900 mm的大型铸钢件,在清理、 精整过程中,仅因轻微的撞击就有几率发生脆断。铸态 下的铸钢件有几率发生这种脆断,也可能见于热处理后。 从断口上看,这种脆性断裂是沿晶界发生的,具有粗 大而光滑的晶面,故称之为“石状断口” 。早先以为这 是因氢脆造成的,1947年才确认,导致此种缺陷的主 AlN 要原因是氮化铝 ( ) 脆性。如钢中氮含量高,终 脱氧时加铝又多,就可能在铸钢件凝固的后期沿晶界 析出AlN,呈网状,致使铸件脆断。 由于铝脱氧效果好,炼钢工人为确保铸件不产生 气孔,随意多加的情况很常见。同时,无论是电弧炉 炼钢、还是感应电炉炼钢,如不采取比较特殊措施,钢液 中氮含量一般都在0.01%左右,冶炼条件差时还会高于 此值。这种情况下,如加铝量太多,就也许会出现石状 断口。为避免铸钢件产生石状断口,严控加铝量 上限值十分必要,一般应在0.12%以下,最高也不能超 过0.14%。 加铝脱氧的方法和保持铝的收得率稳定,也是应 十分关注的问题。铝密度不到钢液的1/2,很易浮在液 面上、被炉渣包裹,不能充分与钢液作用。出钢过程
钙在钢液脱氧方面的应用 随着对铸钢件质量发展要求的日益提高,一些高档次 铸件,只用铝进行终脱氧已不能够满足要求,因此,用 铝、钙复合脱氧受到广泛重视。终脱氧时,将铝、钙 配合使用,不仅可逐步降低钢中氧含量,且还可改 善非金属夹杂物,但由于钙密度仅是钢的1/5,沸点为 1 492 ℃,低于钢液温度,且其活性很强,用于炼钢时 很难准确加以控制。这一制约因素,限制了钙在铸钢 方面的推广应用。近20多年来,对钙在钢中作用的认 识不断深化,应用工艺方法也逐步成熟,现在,可说 是进入实用阶段了。 () 钙的脱氧作用 1 从氧化物标准生成自由能来看,钙脱氧能力强于 铝和镁,但钙在钢中溶解度很小,且沸点又比钢液温 度低得多,如单独用钙脱氧,则钙很难与钢液中氧充 分作用。对含高镍、高锰的钢种,由于钙在其中的溶 解度较高,脱氧效果也较好。 铝和钙配合使用,有互补增益的效果,可将钢中 的氧含量降低到0.002%以下。不仅可有很大效果预防铸件产 生气孔,还可因降低钢中溶氧量和夹杂物含量而改善 钢液流动性,提高铸件表面上的质量。 () 钙对非金属夹杂物的作用 2 用铝脱氧,在钢中形成的夹杂物Al2O3非常细小, 不易上浮而进入熔渣。钢中加钙后形成的氧化物CaO可 以与Al2O3作用,形成多种铝酸钙,颗粒增大,易于上 浮。有的铝酸钙在炼钢温度下为液态,还易于携带其他 夹杂物上浮。故钢液中加铝后再加入钙,可明显提高非 金属夹杂的脱除速率。有研究工作表明,对碳含量低的 钢种,只用铝终脱氧,无论采取何种措施,都不足以避 免产生Ⅱ -型非金属夹杂物。对铸件质量发展要求较高时,加 钙处理更十分必要。有报道:用铝终脱氧的钢,再加 钙处理,静置2 min后,钢中氧化物夹杂总量可减少 60%~70%。美国一铸钢厂的试验根据结果得出,钢液加钙 -型, 处理后,由于非金属夹杂含量减少,且形态为Ⅰ 钢在-18 ℃下的冲击韧度值平均提高70%。 () 加钙方法 3 用钙处理钢液虽有很多好处,但由于钙密度小、 沸点低、活性强,实际应用有很多困难。为此,开发 了多种向钢中加钙的方法,如喷粉法、喂线法、铝弹 投射法和直接加入合金的方法。最简便的方法是将钙 与其他元素配成合金,降低其活性,以便直接加入钢 液中。这种方法较适于用小型熔炼设备的铸钢厂。 1.6
硅钙合金是熔炼铸铁常用的合金,但在炼钢温度 下,硅钙合金活性太高,直接将其加入钢液,因反应 强烈,效果不稳定。以一定量的钡取代硅钙合金中的 钙,可明显降低合金活性,能较好地用于处理钢液。 在此条件下,钡的最大的作用是作为缓冲剂。即使采用 加有缓冲剂的合金,钙的收得率也远低于用喷射法加 入的硅钙合金,对此应心中有数。 美国联合碳化物公司 ,早已生产硅-钙-钡合金 (Calsibar ,作为处理钢液的脱氧剂。由于钙和铝配 ) 合使用有互补增益的效果,硅-钙-钡合金通常都和铝 配合使用。为现场使用起来更便捷起见,后来又生产一种名 称为“Hypercal”的硅-钙-钡-铝合金。这两种含钙合 金的密度都高于硅钙合金,活性低于硅钙合金,可 在出钢时将块状合金投入钢液中,操作较方便。虽 然这两种合金中的钙含量较硅钙合金低,但加入钢 液中的收得率较高,可减少钙的加入量,且处理效 果更为稳定。 用硅-钙-钡合金处理钢液时,合金最好在加铝后 加入,也可与铝同时加入。对不同钢种,用量不完全 相同,可作以下考虑:对碳钢和低合金钢,每吨钢液 可加入0.5 kg铝和2~2.5 kg硅-钙-钡合金;钙在奥氏体不 锈钢中的溶解度较高,加钙还可改善钢液流动性,为 得到最佳流动性,一般可只加硅-钙-钡合金,不再加 铝。为充分脱氧、防止铸件产生气孔,可适当增加合 金用量,如每吨钢液可加合金2.5~3.5 kg;对铁素体不 锈钢,由于钙溶解度低,不加铝就不能得到满意脱氧 效果。 硅-钙-钡-铝合金用于碳钢和低合金钢时,每吨钢 液用量约3~4 kg,一般不必再另外加铝。用于超低碳 铁素体不锈钢时,在大多数情况下要再补加少量铝。美国联合 碳化物公司生产的两种含钙合金的化学成分和密度见 表1。目前,我国也有成分相近的合金供应。
钢业界早已成为常规。按额定容量超20%装料的电弧 炉,简直是凤毛麟角,极为罕见。5 t电炉装料8 t早已 是“小菜一碟” ,装10 t、甚至12 t,也并不稀奇。我曾 拜访不少铸钢厂,言谈之间,似乎都把扩容当作是一 种善举而为之。多年来,我一直在“杞人忧天” ,天倒 是没有塌下来,可我的疑虑始终没有打消。使我放心 不下的,主要是以下说到的两个问题,还有别的一些 “鸡毛蒜皮”的考虑,姑且不说。
关于能耗问题 电弧炉炼钢是能耗很高的作业,节能是一重要课 题。根据电弧炉的特性曲线确定作业电流,并按熔炼 各时期的特点确立用电规范,是节能的重要措施。目 前,我国铸钢行业所用的电弧炉数量很多,却很少有 测定炉子特性曲线是交流电弧炼钢炉的用电特 性曲线 电压一定时,随电流增大,来 ) 自电网的功率P1增大。到达P1曲线的峰值以后,由于 设备的功率因数降低,无功功率增大,P1 不但不 增 大,反而急剧下降。可见,盲目增大电流不仅无益, 而且对电网和设备都非常有害。 () 实际上用于炼 2 钢的有用功率P2的峰值与P1峰值所对应的电流并不一 致。P2峰值对应的电流I0,一般都小于P1峰值所对应的 电流Io′。P1最大时,由于电器设备的阻抗而损失的功 率P3增大、效率η下降,有用功率P2并不最大。因此, 电弧炉运行的作业电流应该是I0,无论如何也不应超 过Io′。 () 目前还不可能用仪表显示有用功率P2、并 3 用以控制电炉的供电,一般都用电流控制。电流控制 是灵敏的,但是,如无特性曲线为依据,就可能会引起 效率降低,电耗增大。例如,当作业电流为I1时,认 为功率不足而增大电流,当然是正常的,但是,如果 简单地将作业电流增大到I2,输入的功率大幅度增加, 而有用功率并未增加。 此外,电弧炉炼钢过程中,还应根据每一熔炼阶 段的炉况确定作业电压,以减少热损失、并提高炉衬
由于钙活性很强,向钢包中加入含钙合金,钙的 收得率可能因操作不严格而有很大的差异,一定要杜 绝操作中的随意性。必须将块状合金投入钢液流中, 不可在出钢前投入空包内,也不可随意投在熔渣面上, 否则,不仅浪费合金,并且不可以保证铸件质量。作业 不当时,往往会产生大量白烟。
的寿命。作业电压愈高,则输入功率愈大。但电压愈 高,则电弧愈长,对炉墙、炉盖的辐射增强,热损失 增大;只有在熔化期间,电弧埋入炉料后,才可用最 高电压,正好这时需要最大的功率;氧化期间,钢液 处于沸腾状态,而且炉渣的黑度系数大,易于吸热, 电弧的能量较易于传递到炉渣和钢液,可用较高的作 业电压。由于此时电弧是的,不宜用最高电压。 还原期间,钢液静止,不利于提温,且此时炉渣黑度 系数小,易反射电弧热量于炉衬、炉盖,应避免电弧 太长,宜用低电压作业。 按理说,每一台交流电弧炼钢炉,安装好后, 都应根据电气设备配置的详细情况,通过短路试验测 定线路的基本信息参数,再计算每一电压下线路的平均参 数,画出每一级电压下的用电特性曲线。每一铸钢厂 都应按照电炉设备特点和所炼钢种冶炼要求,制定合 理用电规范,规定冶炼各阶段作业电压。再根据电炉 在每一种电压下作业时的特性曲线,规定作业电流。 据初步估算,如采用合理用电规范,每吨钢电耗至少 可降低5%。迄今为止,我国铸钢业界还很少有人关注 这方面工作,但随着节能要求日益严格,普遍制订用 电规范的日子必然不会太远了。 现在就应思考的问题是:每一台电弧炉,变压 器和相关的供电设施都是按炉子的额定容量配置的, 电压不可能随意改变。大幅度扩容后,势必要增加能 量输入,电压变不了,只能尽量增大电流。盲目增大 电流,必然导致无功功率增大,电效率降低,单位产 品能耗大增,而且,会使炉衬寿命减少。 偶尔生产一、两件较大铸件,不得不扩大炉子容 量,以提供足够钢液,作为权宜之计可以。把超量扩 容作为常规,是很不应该的。此外,这样的做法,实际 上是以低功率、超低功率进行冶炼,与当前为降低电 耗而向高功率、超高功率发展的趋势背道而驰。其他 国家,电弧炉扩容,一般都不超过额定容量20%。我 认为,现在应该认线
别是采用熔模铸造工艺的企业大多数都采用感应电炉, 用感应电炉炼钢的技术也有了相应发展。现在,制造 铸钢件常用的一些钢种,如碳钢、低合金钢、各种高 合金钢和镍基合金等,都可以用感应电炉熔炼。这里, 简单说说感应电炉炼钢中的几个问题。
扩容过多有损钢液的冶金质量 电弧炉炼钢过程中,一些主要的冶金过程,如钢 液的升温、脱磷、脱硫、脱氧、脱除非金属夹杂物等, 都通过钢液/炉渣界面进行。钢液与炉渣间的界面面积 越大,越利于各种冶金反应进行。为此,渣线处的炉 缸直径与熔池深度之比应保持一个合理的值,一般应 该是5∶1左右。若熔池太深,则不利于钢液温度的控 制,脱磷、脱硫、脱氧、脱除非金属夹杂物等过程也 都受到制约,势必使钢液冶金质量低下。 由于炉壳直径固定,扩大容量只能靠增大炉缸深 度。大幅度扩容,必然大幅度减少钢液/炉渣界面面 积,使熔炼过程接近于简单的熔化。这样做,实际上 是舍质而求量。 2.2
耐火材料 感应炉坩埚所用的耐火材料品种很多,按其性质可 分为酸性、碱性和中性。选用时,主要是根据所炼钢种的 化学成分和质量发展要求,但也要进行成本方面的分析。 炼钢时,钢液温度很高,一般都在1 600 ℃以上, 有时可高达1 730 ℃,且对P、S含量要求较严,炉衬多 采用碱性或中性耐火材料,采用酸性耐火材料者较少。 感应电炉常用的几种耐火材料的性能见表2。 () 酸性耐火材料 1 酸性耐火材料主要是硅砂,主要优点是资源丰富、 价格低,且制成的坩埚耐骤冷、骤热性能好。但 SiO2的熔点低,且在高温下的化学活性很强,能与炼 钢过程中的各种碱性氧化物乃至中性氧化物作用,还 可能被一些活性较强的元素还原。各工业国家,用感 应电炉生产铸钢件的铸造厂,早已不用硅砂炉衬。我 国迄今仍有不少企业采用硅砂炉衬,当然,只能勉强 生产一些低端产品。 () 碱性耐火材料 2 常用的碱性耐火材料是MgO含量为88%以上的冶 金镁砂,由菱镁矿高温煅烧而制成。我国铸钢厂所用 的感应电炉,用镁砂作炉衬的很多。将镁砂置电弧炉 中重熔,可使其中SiO2、Fe2O3等杂质的含量降低,得 到纯度更高的电熔镁砂。电熔镁砂多用于制作真空感 应电炉的炉衬。纯氧化镁材料的线胀系数大,制成的 坩埚易产生龟裂,间歇作业的炉子情况尤为严重,因 而,通常只用于小型炉。 () 中性耐火材料 3 氧化铝和锆砂都属于中性耐火材料,其中应用最 广泛的是氧化铝,很少采用锆砂作炉衬材料。单用氧 化铝作炉衬材料,抗裂和防止酸性炉渣侵蚀的能力较 强,但不适于造碱性炉渣。且由于烧结性能较差,炉 衬寿命不高。 () 尖晶石系材料 4 尖晶石矿物具有类质同象特征,品种很多,成分也 较复杂,用作感应电炉炉衬材料的主要是镁铝尖晶石 ( MgO Al2O)。镁铝尖晶石中MgO含量不到30%,但仍 · 3 属于碱性耐火材料。尖晶石系材料的耐火度高,热膨胀 系数小,目前广泛用作铸钢用感应电炉的炉衬材料。实 际生产中所用的镁铝尖晶石系材料,往往并非全部用尖 3.1
晶石,主要是以氧化铝为基,在其中配加8%~15%的氧 化镁,以便烧结时在氧化铝颗粒之间形成镁铝尖晶石 网络,起结合作用,提高炉衬寿命。加入硼酸后,在 1 300 ℃左右即可形成尖晶石网络。美国铸钢行业所用 感应电炉,大都采用这类材料。用氧化镁筑炉衬时,也 可以配加22%左右氧化铝,形成尖晶石网络。 冶炼合金钢时,也可用镁铬尖晶石 ( MgO Cr2O) · 3
系材料作炉衬,但采用者较少。2009年,德国Erwin Dotsch 编 写 的 《感 应 电 炉 熔 炼 和 保 温》 (Inductive Melting and Holding 一书,在炉衬材料一节中,只提 ) 到两种材料:一种是硅质材料,用于铸铁;另一种是 尖晶石系材料,用于铸钢。美国联合矿产公司、法国 米纳克矿业公司供应的用于炼钢感应电炉的耐火材料, 主要也是以氧化铝为基的尖晶石系材料。
注:①在196 kPa压力下的软化温度;②除另有注明者外,均为20~1 000 ℃间的平均值。
氧化法炼钢 氧化法一般只用于碱性炉。由于感应电炉炉衬的 厚度受到制约,氧化过程中只能保持温和的沸腾,因 此,最好用铁矿石作为氧源,不宜采用吹氧气氧化的 方式,以免激烈的沸腾损坏炉衬。优质铁矿石是最常 FeO 用的氧源。如果来源方便,轧钢时产生的铁鳞 ( ) 也是很好的材料。美国氧化镍 ( ) 易于购得,炼 NiO 含镍钢时就常用氧化镍作为氧源。铁矿石用量一般为 金属炉料的1%~2%,炼碳钢、低合金钢时取较低值, 不锈钢则取较高值。装料时先加入少量渣料和部分铁 矿石,其余在熔池形成后分批加入,以保持温和沸腾 为原则。如果沸腾激烈,可投入硅铁或铝块止沸。 感应电炉采用氧化法熔炼时,脱碳量很少,但这 种温和沸腾可使钢中氢、氮含量明显降低,具有精炼 作用。在难以得到优质炉料的情况下,效果尤为明显。 氧化法可用于碳钢、低合金钢和各种高合金钢,有一 定的脱磷、脱硫作用。 3.3 脱氧 感应电炉炼钢时,炉渣温度低、粘度高、渣量少, 且钢/渣界面小,不可能做到以扩散脱氧为主,通常都 是采用综合脱氧方式,且以沉淀脱氧为主。对于多数 钢种,都用Si和Mn进行预脱氧,终脱氧以铝为主。对 于低碳钢,预脱氧时也用一部分铝。虽然Al2O3的熔点 很高,颗粒也细小,但Al2O3容易与CaO、SiO2、MnO 等氧化物结合,形成低熔点化合物聚集、上浮,预脱 氧时采用部分铝也可行。 3.2
钢液预脱氧后,应经常往渣面上撒炭粉、硅铁粉, 保持还原性气氛。由于对钢的脱氧程度要求日益严格, 感应电炉炼钢时,出钢前炉渣中FeO含量也不可超过 0.5%。终脱氧往往不单是用铝,而是用与各种含钙合 金配成的复合脱氧剂。
关于吹氩精炼 一些铸钢厂采用不氧化法熔炼时,为降低钢中气 体和非金属夹杂物含量,在炉底装多孔塞,进行吹氩 精炼。采取这种措施,立意当然很好,但应认真考核 精炼效果。有研究报告说,无论在炉内或钢包中,单 纯吹氩时产生的气泡较大,上浮快,精炼效果不明显。 3.5 加钙精炼 用感应电炉熔炼时,加钙处理是一种效果很好的 精炼工艺,国外铸钢厂家采用者已很多。这一工艺的 要点见前节。 3.4
液、电弧炉扩容超装弊端及使用感应炉可能碰到的一 些问题,谈了些个人的浅见。我认为,这些乃是铸钢 业界普遍会遇到的事情,很需要我们来关注。在此“抛砖引 玉” ,旨在通过坦诚的交流,获取真知灼见,进而从源 头上把铸钢件的产品质量搞上去,那才是真格的。
- 电话:15028752820
- 邮箱:info@zhugang.com
- 地址:河北省泊头市千里屯工业区199号
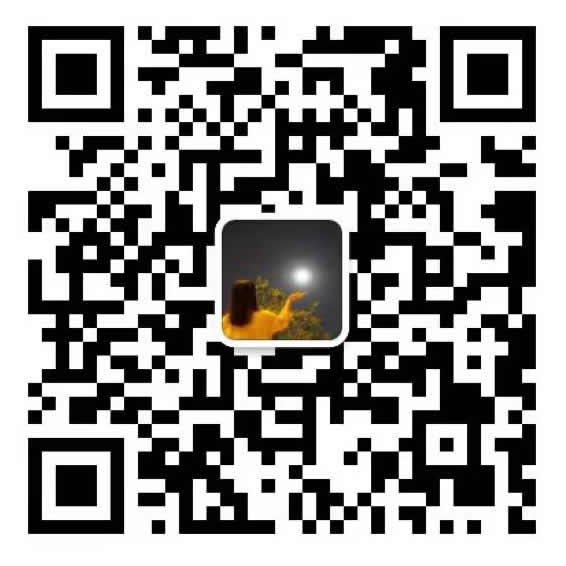
冀公网安备 冀ICP备17001371号-5
Copyright © 2002-2020 bob官方平台app_bob线上官网 版权所有 XML地图