铸钢件脆性断口的成因分析及解决对策
更新时间:2025-04-28 12:22:31
作者: 传动机械设备铸件
摘 : 分析了铸钢件脆性断口的形成原因 , 就铝的氮化物对铸钢脆性断 要 口的影响提出了解决对策 。 关键词 : 铸钢 ; 脆性断口 ; 对策 中图分类号 : TG142. 1 3 文献标识码 : B
铝量过低会影响钢中酸溶铝的含量进而影响钢液的脱氧程度 。钢中残铝量 过高除了会影响钢中夹杂物形态和分布外 , 还会大幅度提升脆性断口发生的 可能性 。有研究者对某个钢种中氮和铝的浓度积进行研究得出钢中氮含量 与加铝量之间的关系 : [ %N ] = 0. 345A l2 - 0. 066A l 0. 0102。 通过这一关系式 ,证明了加铝量在某个范围内可使钢中氮含量达到最 低 。经计算 ,结合实践操作中锰和硅的顺序脱氧效果 ,在不加入其他终脱氧 剂的前提下 ,建议铝终脱氧加入量应控制在钢水量的 0. 08% ~0. 12%之间 为宜 。 2. 2 采用硅钙或稀土金属替代或限制用铝终脱氧 近年来 ,国内外有些铸钢生产企业为防止脆性断口同时为确保不发生 气孔缺陷 ,采用了以硅钙或稀土金属为基本成分的复合脱氧剂来替代或限 制用铝终脱氧 。实践证明 ,通过复合脱氧剂处理后 , 氮化铝消失 , 形成一种 球形复合夹杂物 ,达到了消除脆性断口的目的 。 通过对铝终脱氧 、 硅钙复合脱氧剂终脱氧 、 稀土金属复合脱氧剂终脱 氧、 硅钙合金 铝终脱氧作对比试验分析 ,可以认为对于脱氧效果来讲两 种复合脱氧剂最好 ,但稀土金属复合脱氧剂对加入量的控制要求高 ,易形成 大颗粒稀土夹杂物 ,对于一般用途铸钢件来讲不建议采用 。硅钙复合脱氧 剂和硅钙合金 铝终脱氧其脱氧效果和夹杂物形态能够很好的满足目前普遍采用 的铸钢件钢种 ,可以替代铝终脱氧 。图 2 为包内投铝饼终脱氧工艺铸钢铝 含量对比 ,图 3 为包内喂硅钙线和铝线终脱氧工艺铸钢铝含量对比图 ,其中 # # 1 样为终脱氧后钢包内取样光谱分析 , 2 样为浇注 3 /4 时铸钢件取样光谱 分析 。 从图中可见 ,同一技术方面的要求 (A l: 0. 020% ~0. 060% )下利用包内喂硅钙 线和铝线终脱氧工艺与包内投铝饼终脱氧工艺相比存在以下明显优势 : 一 是在钢液终脱氧程度上包内投铝饼终脱氧工艺明显出现了浇注过程的二次 脱氧或铸型里的三次脱氧 ; 二是在残铝量控制精准度方面包内喂硅钙线和 铝线终脱氧工艺优于包内投铝饼终脱氧工艺 ,且包内投铝饼终脱氧极易出 现铸件中残铝量超下限的现象 ,为保证铸件残铝量达到技术方面的要求而增加投 铝量就会增加氮化铝析出的机会 , 给脆性断口的发生带来更大的可能 。因 此 ,对于一定要采用铝终脱氧的钢种或工艺 ,建议采用硅钙合金 铝终脱氧 , 由于在钢液凝固过程中 Ca2 N2 领先于氮化铝析出 , 不会对晶间的结合力产
生较大影响 ,因此在不改变现有工艺的前提下 , 推荐采用减少出钢铝加入 量 ,取消包内投铝 ,增加包内加入硅钙或喂硅钙线工艺来控制残铝量达到防 止脆性断口的目的 。
图 2 包内投铝饼工艺铝含量对比 3 图 包内喂硅钙线和铝线工艺铝含量对比
时便析出氮化铝夹杂物 。 众所周知 ,钢中氮含量与钢 的冶炼方法有着必然的联系 , 一 般转炉钢氮含量为 ( 20 ~ 40 ) × -6 10 左右 , 平炉钢氮含量为 ( 50 ~70 ) × - 6左右 , 电弧炉炼钢 , 10 氮含量一般为 ( 80 ~120 ) × - 6 10 图 1 脆性断口 左右 。 在铸钢件生产领域 , 目前普遍采用的冶炼设备为电弧炉或感应电炉 。 其钢液中氮含量相比来说较高 ,这给氮化铝的形成创造了一个有利条件 。而对 于炼钢方法来讲 ,目前终脱氧工艺一般都会采用铝终脱氧 ,只有少部分铸钢企业 采用复合脱氧剂进行终脱氧 。因此无论是电弧炉还是感应电炉炼钢 , 铝终 脱氧工艺的采用 , 给氮化铝的形成提供了足够的冶金条件 , 只要钢中 [ % A l] ・ [ %N ]浓度达到一些范围氮化铝必将形成于奥氏体晶界 。因此钢中 氮和铝的浓度成了铸钢件会不会产生脆性断口的决定性因素之一 。 2 铸钢件脆性断口的防止方法 2. 1 控制钢中氮含量和适宜的残铝量 铸钢中的氮含量与铸钢冶炼工艺 、 操作 、 原材料选用等有着密切的联 系 。对于电弧炉冶炼而言 ,降低钢中氮含量的最直接的方法有 : (1) 严控废钢的清洁度和干燥度 。 ( 2 ) 保持充足的氧化沸腾时间和速度 ,有利于气体的排出 。 ( 3 ) 在扒渣 、 搅拌过程中最好能够降低或避免钢液 ,减少钢液吸气 。 ( 4 ) 在保证脱氧效果的前提下 ,尽量缩短还原期时间 。 ( 5 ) 采用气体保护出钢和保护浇注以减少出钢 、 浇注过程吸气 。 ( 6 ) 采用真空除气的炉外精炼手段降低气体含量 。这是去除钢液中气 体的有效方法 。 对于感应电炉而言除了控制好与电弧炉相关点外 , 控制钢中氮含量的 重点是严控入炉废钢中的氮含量 , 尤其是返回料的加入量一般不能 超过 50% 。 由于铝终脱氧铸钢中铝的存在是必然的 , 根据许多研究者的分析和实 践 ,铸钢中残铝量一般应控制在 0. 025% ~0. 050%之间为宜 。因为钢中残
另外也有一些铸钢件生产企业采用钛和锆替代铝进行终脱氧 ,虽然钛 和锆可以固氮 ,氮化钛可细化晶粒 , 可影响磷共晶的分布 , 但需要严控 钛的加入量 ,否则碳和硫的钛化物会产生另一种晶间破裂 , 其危害相当严 重 。锆的情况与钛基本相同 。 图 4 给出了低合金钢中奥氏体中析出氮化铝的边界条件 , 双曲线下部 为溶解在钢中的氮和铝的共存区 ,上部为氮化铝的析出区 。 综上所述 ,在铸钢中含氮 量较高的情况下 ,如果残铝过 高 ,确实易产生脆性断口 , 但铸钢中残铝量和含氮量对 脆性断口的影响与钢种特点 、 铸件壁厚和铸件大小等多种 因素相关 ,故不能断言其含量 高就必然产生脆性断口 。对 图 4 、 氮 铝在低合金钢中的溶解度 于目前铸造碳钢和低合金钢 ( KA lN = 2. 3 × - 4 ) 10 -4 而言 KA lN = 2. 3 × 10 。只要 控制好钢中氮和铝不超过 KA lN的平衡值就能够尽可能的防止氮化铝的形成 , 从而减 少或消除脆性断口发生的可能性 。□ 收稿日期 : 2009 - 03 - 26
因此对于一定要采用铝终脱氧的钢种或工艺建议采用硅钙合金铝终脱氧由于在钢液凝固过程中ca2n2领先于氮化铝析出不会对晶间的结合力产3设计研究铁道机车车辆工人第6期2009年6月生较大影响因此在不改变现有工艺的前提下推荐采用减少出钢铝加入量取消包内投铝增加包内加入硅钙或喂硅钙线工艺来控制残铝量达到防止脆性断口的目的
脆性断口是铸钢件常见的一种宏观断口 ,断口的特点为脆性断裂 ,因此 这种断口一般被称为脆性断口 。目前在不同的国家和地区 , 对这种断口的 叫法各不相同 。如国际铸造缺陷图册中称其为“ 岩状断口 ”也有人称其为 , “ 亮斑断口 ” 贝壳状断口 ”由于这种断口是沿一次奥氏体晶界破裂 ,即晶 ,“ , 间裂纹 ,所以也有许多学者称其为“ 晶间裂纹断口 ” 。 铸钢件产生脆性断口的原因众说不一 ,有的研究者认为 ,脆性断口是由 于钢中氢量高和奥氏体相变应力所造成 , 而有一些研究者认为是由于铸钢 件凝固过程中钢中析出铝的氮化物所致 。本文结合多年实践经验就铝的氮 化物对铸钢脆性断口的影响及防止方法做个简要分析 。 1 铸钢件产生脆性断口的原因 铸钢件脆性断口的特征为 : 断口表面为平滑 、 光亮 、 稍有弯曲的小平面 组成 ,貌似岩石断口 ,如图 1 所示 。许多研究已证实 , 铸钢件产生脆性断口 的原因是由于在一次奥氏体晶界上析出氮化铝而使晶界脆化 。氮化铝在奥 氏体晶粒形成时以粗大薄膜状析出于晶界 ,产生组织缺陷 ,降低铸钢的塑性 和韧性 ,增加晶间产生裂纹的倾向 。这种粗大薄膜状氮化铝与其他弥散分 布的夹杂物不同 ,其形态是厚度为 0. 05 μm ,其他尺寸不大于 5 μm 的薄膜 , 这种形态的氮化铝夹杂物沿晶界分布 ,大大减弱了晶间的结合力 ,进而影响 铸钢的力学性能 。 铸钢中氮化铝的溶解度取决于它们的浓度积 KA lN = [ %A l] ・ [ %N ]。 当铸钢中 [ %A l] ・ [ %N ]超过 KA lN平衡值时 ,在 800 ℃~1100 ℃ 左右
- 电话:15028752820
- 邮箱:info@zhugang.com
- 地址:河北省泊头市千里屯工业区199号
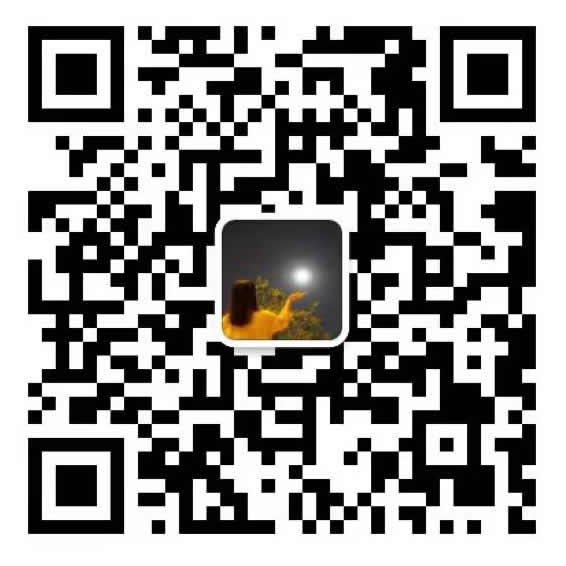
冀公网安备 冀ICP备17001371号-5
Copyright © 2002-2020 bob官方平台app_bob线上官网 版权所有 XML地图